Lafarge
Lafarge, now known as Tarmac, is one of the UK’s leading aggregate suppliers, operating 140 plants across the country and transporting over 10 million tonnes of aggregates annually.
The Challenge
Lafarge reached out to us due to the inefficiencies of their outdated legacy systems, which were driving up costs and negatively impacting customer service. They were struggling to secure the right amount of transport to meet customer demands at a competitive price. High operational costs, declining customer satisfaction, increased pressure on the order office, and frequent delays leading to backlogs meant staff were often required to work overtime. It was clear that a change was needed.
How We Helped
We collaborated with Lafarge to define their best practices and business rules, thoroughly identifying and documenting all interdependencies with other systems and processes. We then developed a bespoke ordering system that fully integrated with an off-the-shelf optimisation solution. This new system was designed to manage and allocate transport efficiently, based on daily customer orders.
The Results
The bespoke ordering system we implemented has enabled Lafarge to save approximately £4m annually. Haulage utilisation improved from 50% to 58%, and there’s now more proactive planning and management of resources. Additionally, the allocation of work to hauliers is now fairer and more efficient.
Testimonial
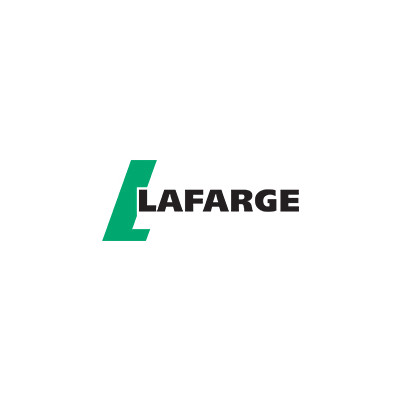
“Evolve applied a professional and thorough assessment of our old system and developed the ideal automated solution. The savings in man hours and problem-solving are huge. I wouldn’t hesitate in recommending them to other businesses.”